伸線加工の仕事をしていると「カッピー断線」というものをたまに聞きます。
カッピー断線は、キズ要因や伸び切れなどの伸線加工で発生する一般的な断線とは異なり、不適切な加工条件が重なった際に発生する特殊な断線です。
この記事では、伸線加工で発生するカッピー断線について原因と対策を解説します。
カッピー断線とは
カッピー断線とは、線の内部に発生した空洞部分(ボイド)が原因で発生する断線のことです。
社内の次工程や客先での、伸線や曲げ加工などで負荷を与えた際に、線内部が空洞のため強度が足りずに断線してしまいます。
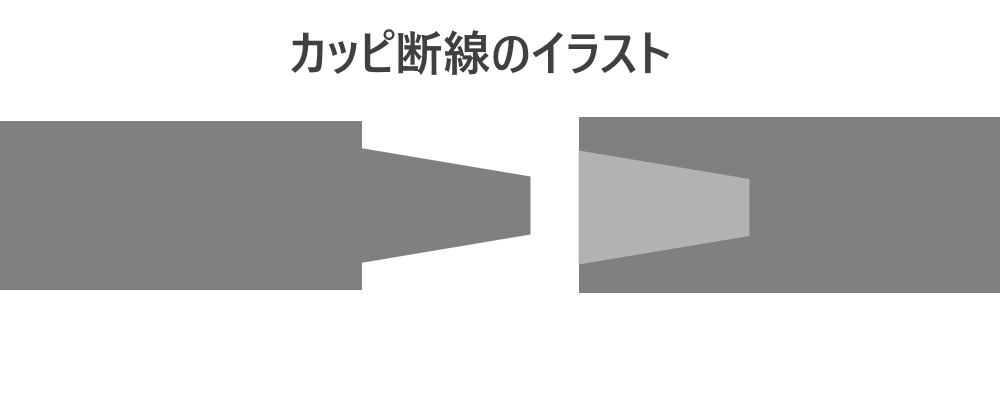
カッピー断線は破断部分が三角形のカップのように切れるのが特徴で、片方が凸で片方が凹の形状になっています。
内部だけが空洞で線の外観を見ても異常品なのか見分けがつかないため客先に流出しやすく、カッピー断線が発生した前後の製品も見た目で判断できないため異常品の疑いがあるということで、その近辺の全ての製品が返品ということにもなりかねません。
カッピー断線の原因
カッピー断線の原因は、線内部の空洞(ボイド)が原因ということを紹介しました。では、なぜそのような空洞ができてしまうのかを解説します。
伸線加工での空洞はシェブロンクラックと呼ばれている
伸線で発生する線内部の空洞は「シェブロンクラック」と呼ばれています。
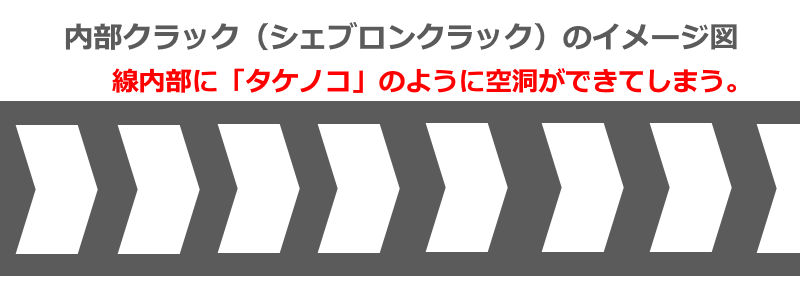
シェブロンとは山形や谷型のV字模様のことで、軍隊などで制服に貼り付ける階級章などもV字の形をしており、これもシェブロンと呼ばれています。
伸線で発生する空洞の形も伸線方向にV字型になっているため、V字の割れというということでシェブロンクラックと呼ばれています。
このシェブロンクラックは、線の外観検査では異常が見られないため、実際に線を切って長手方向に断面を見るか、探傷機という超音波などで、線内部の傷を発見する特殊な装置を使用しないと発見することができません。
シェブロンクラックの原因
カッピー断線の原因であるシェブロンクラックの大きな原因は、大きすぎるダイス角度と小さすぎる減面率です。
ダイス角度が大きすぎると、線の表面の抵抗が大きくなりスムーズにダイス内を進むことができず、線の中心部分だけが引っ張られてしまい、中心部分が限界を迎えると内部だけ割れてしまいし、結果的に内部に空洞が発生します。
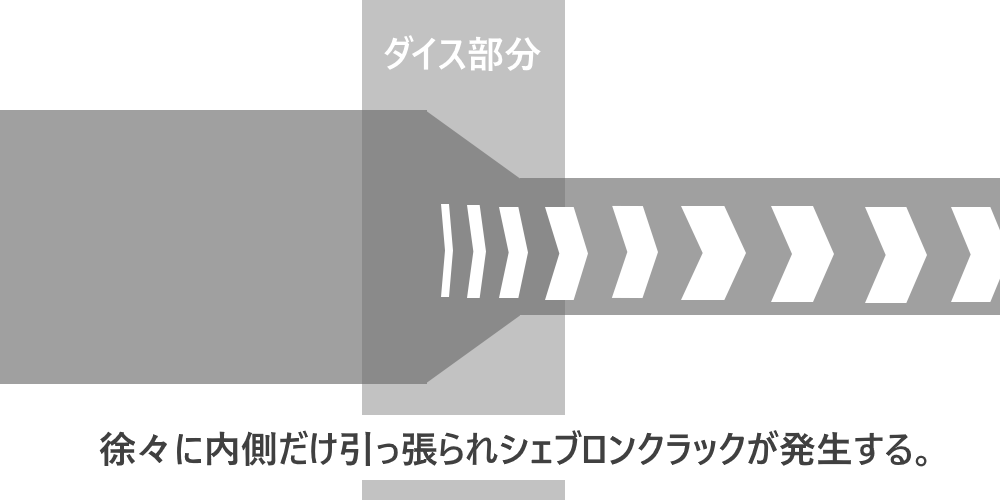
また減面率が小さすぎることで、線の内部まで圧縮されずに線の表面だけ置いて行かれるような加工をされてしまうことにより、線の内部だけ引っ張られてしまい、内部にクラックが発生してしまいます。
ほかの原因として考えられるのが、伸線潤滑剤が加工条件とあっていないために、ダイスと線の間で適切な潤滑効果を得ることができずに、ダイスと接触する線表面がスムーズにダイス内部を進まず、内部だけが引っ張られてクラックが発生していることも考えられます。
カッピー断線の対策
カッピー断線の原因は、線内部に発生したシェブロンクラックなので、シェブロンクラックを予防することがカッピー断線の対策になります。
シェブロンクラックを予防するには先述したとおり、原因となるダイス角度と減面率を見直すこと、または潤滑剤を見直すことで解消が期待できます。
ダイス角度(半角)は一般的に5~9°、減面率は10~30%が良いとされているため、この範囲から外れている場合には、この範囲の伸線ダイスを選定することにより、シェブロンクラックの発生とカッピー断線の予防ができます。
潤滑剤は最適なものを見つけるのは難しいですが、加工する条件(減面率やダイス角度)・材料の種類・乾式or湿式などを潤滑剤メーカーに問い合わせることで、最適だと思われるものを選定してくれるので、実際に試して選ぶ必要があります。
潤滑剤の変更は、ダイス角度や減面率の変更よりも、後工程で影響が出やすいので慎重に行う必要があります。
カッピー断線のまとめ
ここまでカッピー断線についての説明、その原因となるシェブロンクラックについて解説しました。
カッピー断線はシェブロンクラックが発生した際に断線した状態のことを指すため、カッピー断線を発生させないためにはシェブロンクラックを予防することが大切です。
シェブロンクラックのある線は外観では判断がつかないため、製造プロセスで抑制することが必要です。
コメント