減面率(げんめんりつ)とは断面減少率の略称で、加工前の断面積が加工後に、どのくらい小さくなっているかを表す割合のことです。
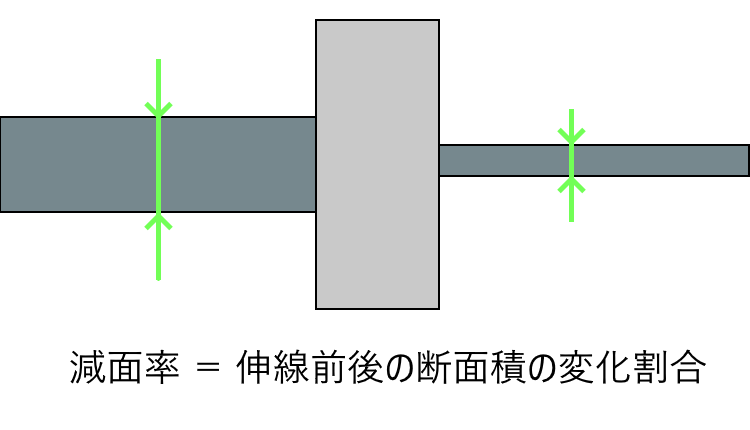
伸線加工では伸線ダイスを通すことで線を細くしていくという加工であり、寸法として求められる部分で変化するのは線径だけなので、この減面率というのが重要視されています。
断面積が減った分だけ長手方向には伸びていきます。
この減面率の設定によって、伸線ダイスの寿命が変わったり、誤った減面率を設定すると不良品が発生することもあります。
この記事では減面率の計算方法から、適切な減面率を設定しないと、どのようなことが起きてしまうのかを紹介します。
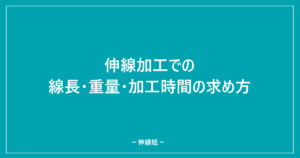
減面率の計算方法
減面率とは加工前の断面積と、加工後の断面積の変化の割合です。

加工前後の断面積の割合を計算するだけなので、それほど複雑ではありません。
ですが毎回手動で計算するのは面倒だと思うので、Excelなどで計算式をセットしておくことをお勧めします。
連続伸線機を使う場合には、式を連続して並べて折れ線グラフを表示しておくと、各伸線機での減面率の変化がわかりやすく、パススケジュールが見やすくなるのでおすすめです。
適切な減面率でないとどうなるのか?
どのような鋼種を使用するのかによっても変わりますが、一般的に減面率は10〜30%の範囲が最適と言われています。では、その範囲を超えてしまうと、どのような問題が発生するのかを3つ紹介します。
- ダイス寿命が短くなる
- 内部クラック(シェブロンクラック)の恐れがある
- 機械負荷が大きくなる
- ダイス寿命が短くなる
-
減面率を適正範囲よりも高く設定することで、ダイス寿命が極端に短くなってしまう恐れがあります。
減面率を高くするということは、ダイス1枚でより細く伸線するということなので、ダイスに掛かる負荷は大きくなり、発熱も大きくダイスが傷みやすくなり摩耗も早くなります。
あわせて読みたい伸線加工の冷却について【行わないとどうなる?】 切削加工では切削油をかけながら、圧延加工では直接水を掛けながらなど、冷却を行いながら加工を行っています。伸線加工も同じく、冷却を行いながら加工を行っており、…減面率が適正範囲内だとしても15%と25%で比較すると、一般的には25%の方がダイス摩耗は早くなります。
減面率を大きくした方が、使用するダイス枚数が少なくなりコストも減るように思われますが、ダイス寿命が短くなり交換頻度が増えてしまうと、結局コストは同等か、それ以上になってしまう場合があるので注意が必要です。
- 内部クラック(シェブロンクラック)の恐れがある
-
減面率が極端に低い場合には、線内部にクラック(シェブロンクラック)が発生し、カッピー断線が発生する恐れがあります。
線の内部で発生するクラックなので、発生しても外観で気付くことは不可能なため流出しやすく、本来求められる引張強さも、内部にクラックがあるので満たす事はできません。
曲げ加工などを行うと簡単に折れてしまったりなど、線自体の品質に大きな悪影響が発生します。
多くの場合では、伸線した線がそのまま最終製品になるということはあまり無いので、自社内の次工程や客先で大きなトラブルになり、大量の返品・不良品を積んでしまうことになりかねません。
- 機械負荷が大きくなる
-
減面率が高くなるということは、1枚のダイスでより大きい加工を行う必要があるため、ダイスから線を引き抜くために必要な力(引抜力)も大きくなります。
伸線機への負担が大きくなり、使用電力が増加したり、長期的に見ると伸線機の各部品の摩耗スピードが速くなったりと、機械トラブルの元となります。
あまりにも減面率が高すぎると、伸線に必要な引抜力が強すぎて伸線機のパワーが負け、ダイスから線を引き抜くことができないという問題も発生します。
ダイス寿命と機械負荷については、すぐに気付くことができ、発生しても自工程内で収められる話ですが、内部クラックについては客先や次工程に流出する可能性が高いので、最も注意が必要な不具合になります。
減面率の変更を行った場合には、断面検査などを行い初期管理をしっかり行う必要があります。
高い精度を求められる製品では、探傷機などを使って内部クラックが無いことを確認することもあります。
また、減面率が大きいと「引き細り」の原因にもなるので注意が必要です。
減面率とは?まとめ
減面率とは何か?というところから計算方法、適切な減面率でないと何が起こるのかを紹介しました。
伸線加工はダイスに線を通すだけというシンプルな加工方法のため、変更できる加工条件の項目は多くありません。
そんな限られた加工条件の項目の中でも、減面率は自由に変えることのできる項目かつ、伸線性にも影響が出る項目です。
適切な減面率を設定して、伸線性の向上を行なっていきましょう。
コメント